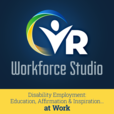
Summary: Note: click image for caption and image details.<br> Hear about Opportunities for Individuals with Disabilities and Reflections on Workforce Development from VMA Workforce Development Director, Katherine DeRosear. <br> Episode 11 Transcript: December 15, 2015<br> Rick (RS)– Welcome to the VR workforce studio, the disability and employment podcast from the Wilson Workforce and Rehabilitation Center. I am your host Rick Sizemore along with the Executive Director of the WWRC Foundation, my co-host Anne Hudlow. Hello Anne<br> Anne Hudlow (AH) – Hello Rick. It is great to be here to creating hope and a path forward so individuals with disabilities can go to work.<br> RS– Anne we have an incredible show today. Key leaders from the Virginia Manufactures Association and the Manufacturing Skills Institute.<br> The episode is from the business industry employer gateway category and we will hear how VMA and MSI have not only developed and in-depth understanding of Virginia’s workforce needs; but, how they have evolved strategies to train and credential the workforce of tomorrow by reducing skills and interest gaps.<br> VMA and MSI are marshalling every available resource and partner in education, workforce development, manufacturing and government to truly build the workforce of tomorrow through effective collaborations.<br> AH –We hear every day about new manufacturing facilities coming on line. Executive Order 23 predicts that we’ll need 1.5 million new workers in just in just the next few years to meet the workforce needs. And, in addition to that we are particularly excited about EO 46 emphasizing the positive contributions that individuals with disabilities can make in the workforce. That combined with the Virginia Board of Workforce Development’s promotion of advanced manufacturing and OFCCP503 regulations for disability employment, have certainly convinced me that WWRC is on the right track. Our foundation is a campion for WWRC as it retools to offer “dreamit”, “doit” academies and start up a career pathway that culminates with the manufacturing technology training program.<br> RS, I caught up with Jim Leech who is heading up WWRC’s MTT program and one of the first steps is training the consumers on the production line.<br> Jim Leech (JL) Yes that is true Anne. The Materials Handling department at WWRC gives our clients many opportunities to learn what job requirements and skill sets are actually required in Virginia businesses and manufacturing. One of these job exercises is setting up and operating a boxed salt transfer assembly line utilizing a roller conveyor which transports cases containing 24 boxes of salt from one end of the conveyor where the salt is unboxed on a table to the other end where the salt is repacked into empty cases on another table. The clients need to organize themselves at each end to make the job exercise the most efficient it can be, which takes coordination between everyone on the line. We actually do a time study to observe how long it takes to do each small step of the process to see what the actual cost would be to accomplish the task as if it were in a real manufacturing facility. The exercise can run several hours and is real work with each carton of salt weighing 25 pounds, with a production rate of about 30 pounds per hour. They learn a great deal through this exercise.<br> AH -Students Jim works with had this to say about the training.<br> Student – We really had to work as a team to understand what the other person is doing in order to keep the product moving on the conveyor.<br> JL-The conveyer system for the new program is going to be a little higher level, it will have a Variable speed drive, and its purpose will be for us to be able to configure a number of different scenarios.<br> AH -If you would like to know more about how you can support us as we help WWRC put people to work, you can conduct me by clicking the foundation link right ...