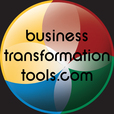
Summary: In This Episode: Today, we conclude this miniseries by looking under the hood at the final steps of ROUTINE: Test, Iterate, Normalize, and Equip. ROUTINE is the backbone tool for process transformation. It is an intrinsic method of improvement that is part of the nature of organizations. Our goal is to make improvement just as much a ROUTINE as payroll and operations. Build the ROUTINE into each of the 4Ps: People, Product, Process, and People, and you will see returns for your business and career that seemed impossible to achieve in all of the daily firefighting. Show Notes BTT 007 – Download Member Content Enhanced Podcast BTT 007 – Download Member Content We hope you are seeing that the tools and tactics in our shows are not overly-complex. In business, the more complex a mess looks, the more simple the solution needs to be. Consider Lean Manufacturing, it is radically simple in its control mechanisms and algorithms when compared to MRP systems and push schedules. Likewise, the complexity of our organizations are best improved with a straightforward tool, ROUTINE, to build improvement into our processes. This will create the healthy processes you need to deliver healthy profits. TESTING: As a chemist working in an aerospace many years ago, I learned the value of testing assumptions. This tradition was not adopted in business. Even in Lean Six Sigma, what we call testing is more like a statistical exercise. Testing in a lab takes a small sample and mixes vial A with vial B to ensure our predictions are correct. In business, we may believe we have identified the root causes, but only after going through a hands-on test can you be certain you have the right root causes, and you understand the per cent contribution of each root cause. Failing to test derails many otherwise excellent projects. We believe our team identified the root causes, we used Fishbones and C&E Matrices, we brainstormed and we even went to the Gemba to go see the work. We are “probably” right. At this point, we need to conduct a test. Six Sigma specialists are trained in Designed Experiments and we are fans of this method because it is the best way to turn knobs and twist dials and see all the interactions, complexities, unexpected outcomes, and outputs. DOE scares many people because the way it is taught is deeply statistical. It is a bit like trying to learn programming before you use Microsoft Outlook. In a future show, we will walk you through what we call simple-DOE, which takes the best fractional designs and Taguch principles, but makes them plug and play. We will provide the templates you need. Yet there is an even more basic tool that we should always use in the testing phase: Piloting. For people I have trained all over the world I show them one of the 10 commandments of a Lean Six Sigma project, “Thou Shalt Do a Pilot!” My most expensive failures occurred because I allowed my teams to simply skip the pilot. We were smart. We were ambitious. We thought we were right. We were dead wrong! The outcome of the testing phase is that we turn assumptions into proofs. ITERATING: This is something that was lost by most businesses who adopted it as a method 50 years ago, when Deming began teaching Plan/Do/Check/Act. Even in Lean Six Sigma projects, when we are working a problem, we have a mistaken belief that we are after “the one solution.” What we actually want is a set of countermeasures that will have various weights in a final solution. This is very different from looking for “a solution.” We use a set of countermeasures to optimize the outcomes we are monitoring. Software and IT solutions are often guilty of this poor belief. We are always looking for that next software solution that will solve our problems. We often end up cementing poor process behavior because it is now hard wired into the programs. A much better approach is to use ROUTINE to install Lean Six Sigma and Theo[...]